
#3d printer slicer for ipad drivers
The printer comes with a hex set, but I bought two additional hex improvements, a hand-held screwdriver, a set of hex drivers to go with it, and a hand-held hex driver set. I started with one box, but it only left a couple inches on the sides, and I planned to rotate my build, so I bought a second box. For the floor I bought a couple boxes of ‘jigsaw’ type padded floor pads from Home Depot. They had no complaints, but this wasn’t their highlights, I suspect. Their previous lives were either the bar during parties, or trade-show foundations for monitors. I had two folding tables for the parts and the parts build. My setup was going to need 3 things initially, a table for the parts, a table for construction of the parts, and a floor mat for the build. I was going to need every BTU in the hottest Summer we’ve had. I live in Florida, and it was Spring/Summer, so I insulated my garage door and set up a 6500 btu AC unit in my garage to augment my 5000 btu AC in my garage shop unit.
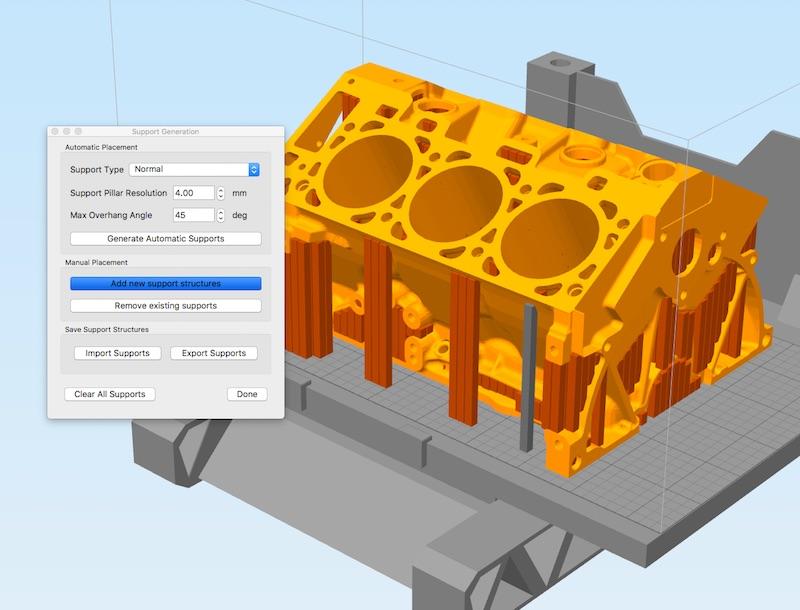
I decided to build my printer in my garage and move it to my shop later. Setup area left, parts table, top right, assembly table, bottom right At one point I hit 13 printers in my shop, and it was plenty noisy on a high-volume day. When I got to six printers, running all the time, it was time to be exiled. Just to be clear, I started with one printer in my studio. So the printer needed to be built in my shop.

So the printer needed to live in my shop, as my doors wouldn’t be big enough to move the printer to move out to my shop. And my wife doesn’t like the constant noise from my printers. But my studio is in the middle of my house. I would have loved to be able to be able to build my Modix in my studio. Also, the printer needs to be built in the room it can fit in. The key to unboxing is to find a room you can take over, possibly for the next month, unless you have a solid block of time to put into construction. The printer arrives…some assembly required I’m just the kind of guy who loves to assemble a grill, dishwasher, and on a good day, a disc brake. It had to be built from the ground up, every motor, every screw, every pulley.Īnd that’s just fine. But this wasn’t a simple unboxing of a project. I had read enough reviews to have a fair idea of what was coming, a pile of boxes, a possibly questionable assembly guide, and some time focus on it for calibration. The printer had the specs I needed for several upcoming large projects. I bought this machine to make big art to satisfy my client’s needs.
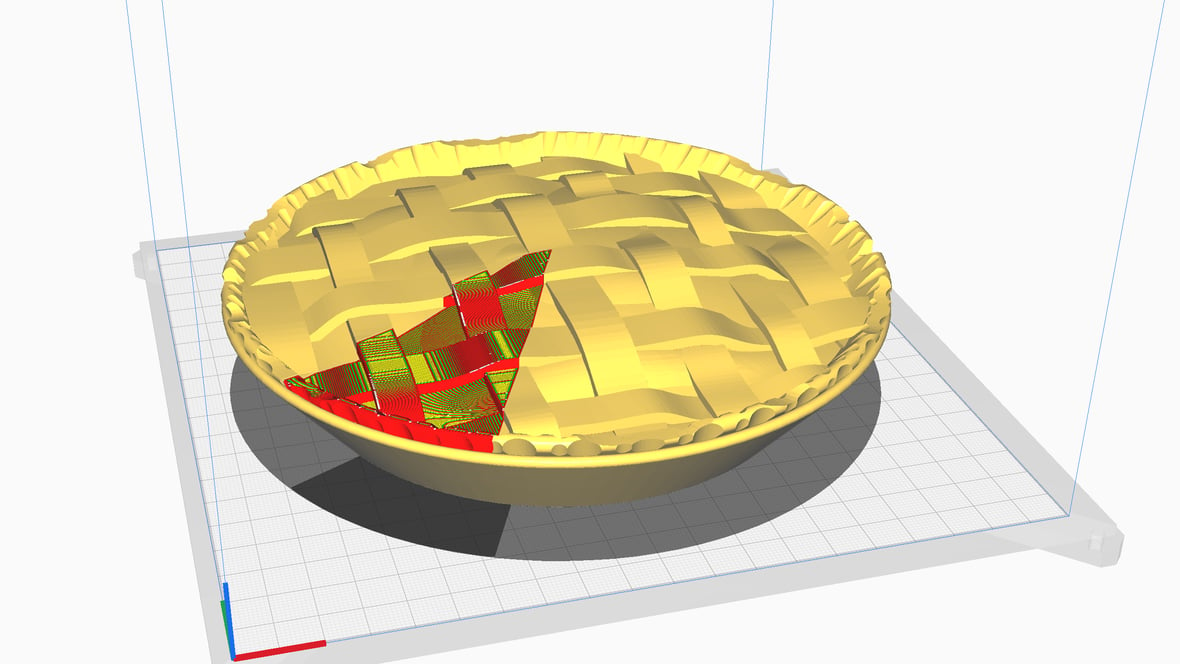
I am an artist who has serious production schedules. This is an early write-up, so I’m not really publishing it yet. There’s not a lot of external support for the machine, so I thought I’d add a page to my site to cover some of the things I’ve found about this incredible printer. The newest addition to my fleet of 3D printers is the Modix Big-60. 3D printing BIG and high quality, who would have guessed?Ĭhurning along with a.
